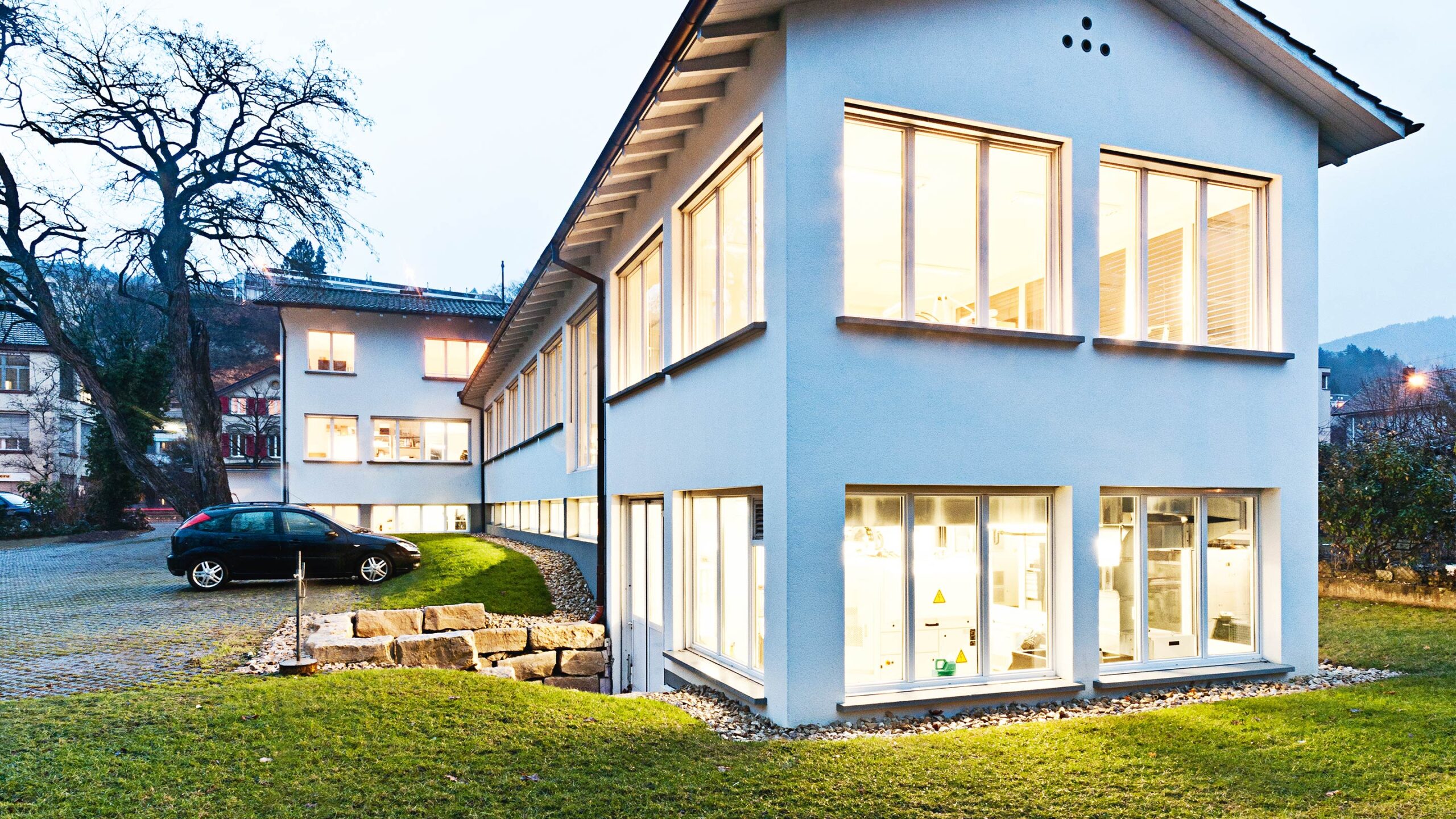
Manufacture
At Armin Strom, we’re obsessed with every detail of every watch that we make. We develop, mill, emboss, galvanize and hand-finish all of our watches in-house. We adhere to the very highest haute-horology standards because we know that Armin Strom collectors appreciate looking at more than just the time.
A watchmaking approach that keeps no secrets.
Armin Strom represents a unique fusion of the swiss-german horological tradition with avant-garde ‘transparent mechanics’ and an unwavering commitment to horological innovation. Our watches are designed to both showcase how our movements actually work and to validate the attention to detail that goes into their production. Whether with a loupe or with the naked eye, with an Armin Strom timepiece there will always be something captivating to see.
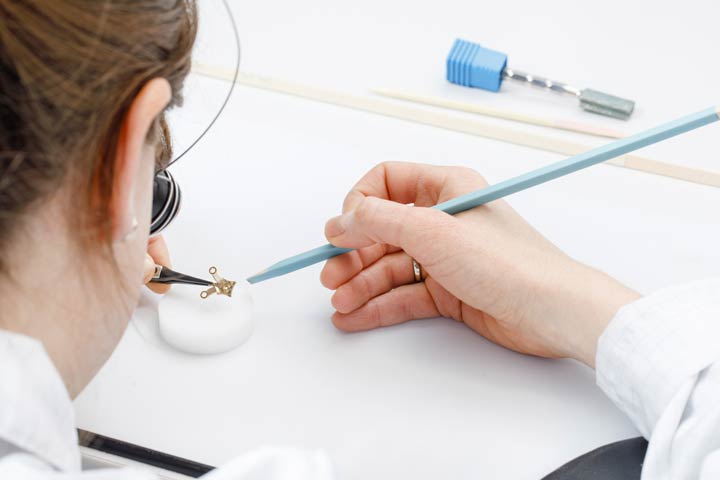
At Armin Strom, our highly qualified and dedicated team invests an incredible amount of enthusiasm, passion and effort to create watches that are mechanically exceptional and meticulously well-finished. “The only difference between the possible and the impossible is that the impossible takes a little longer.” [Mrs. William Tilton, “The Washington Herald”, 1921].
Our passion for ‘transparent mechanics’ is at the core of our watchmaking design philosophy, but perfection in our execution and in the long-term reliability of our watches is always paramount. These priorities are the hallmarks of the Swiss-German watchmaking tradition. We honor that tradition with every watch that we produce at the Armin Strom Manufacture.
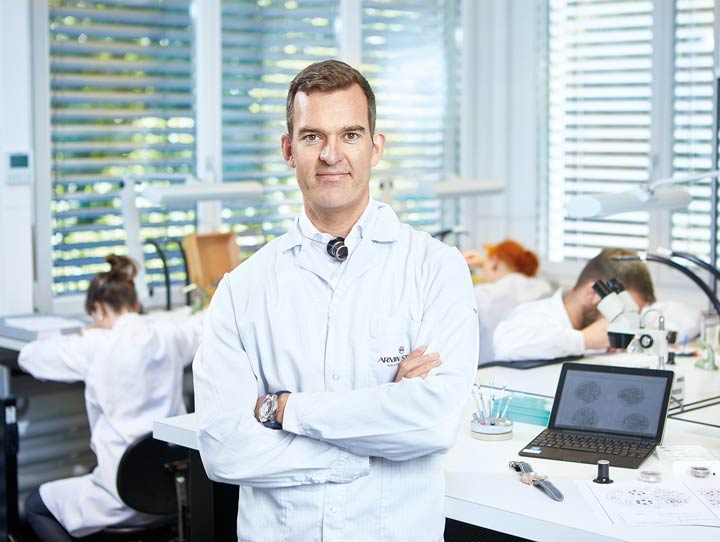
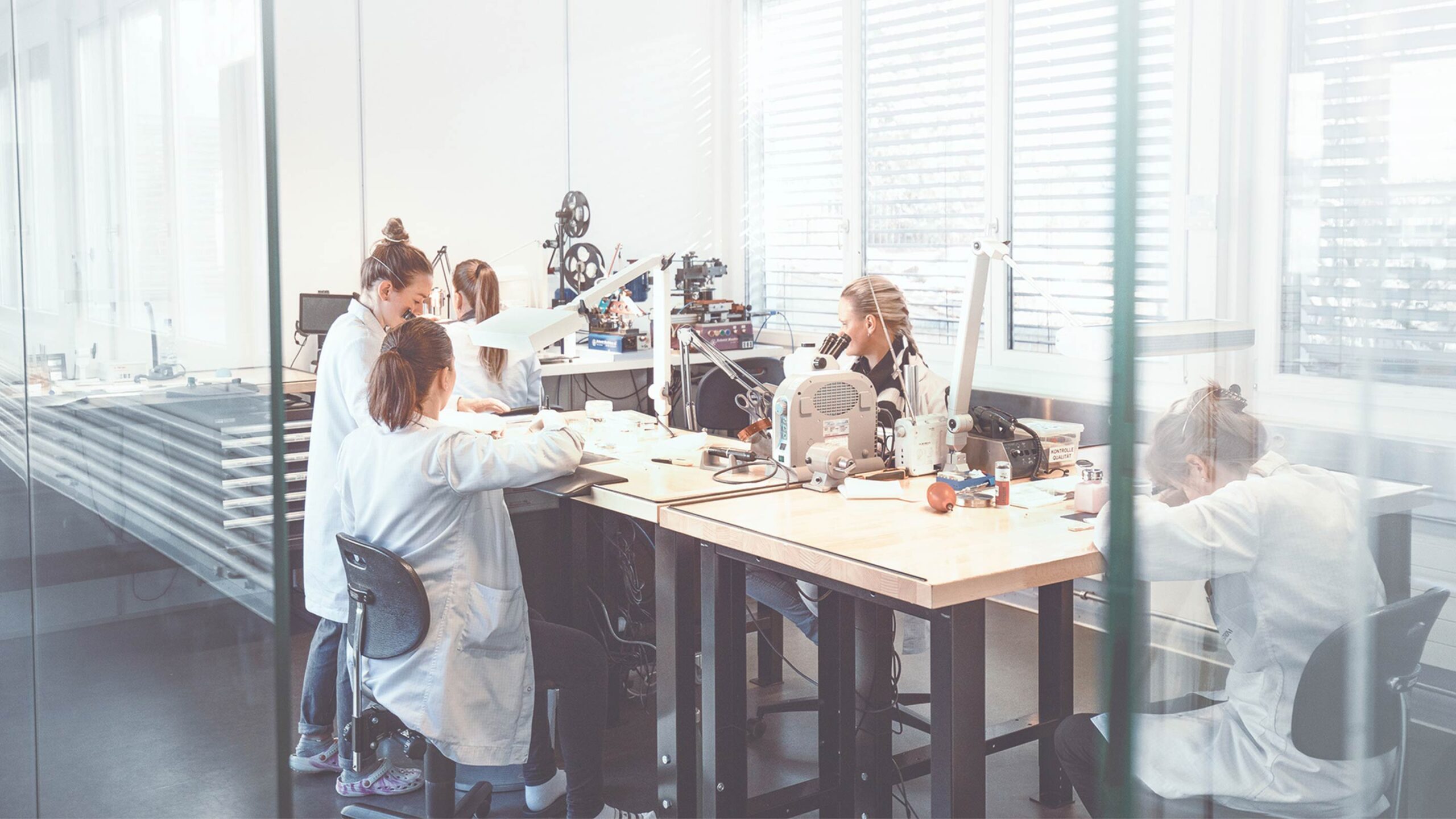
Decoration
The human element elevates watchmaking into mechanical art.
Hand engraving
Every piece is unique.
Steel burins in various sizes and wax-coated holders are the tools of the engraver.
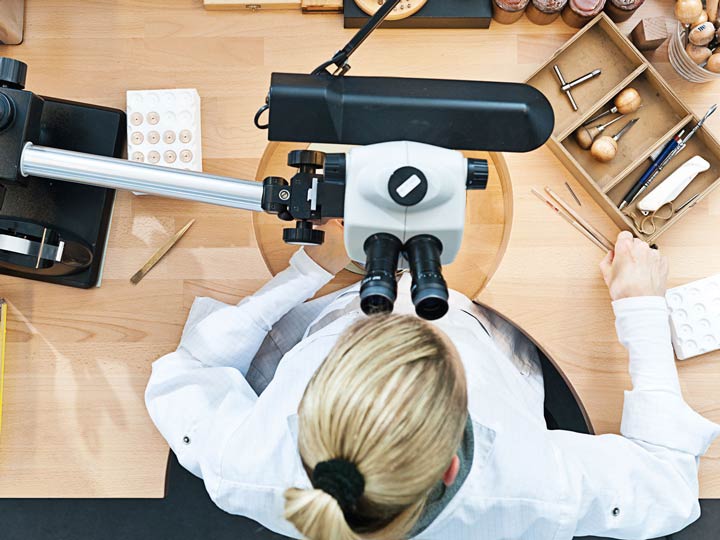
In the engraver’s hands, each workpiece becomes a unique work of art. The engraver draws their own motif design on the workpiece with a needle according to their original drawings; working under the microscope.
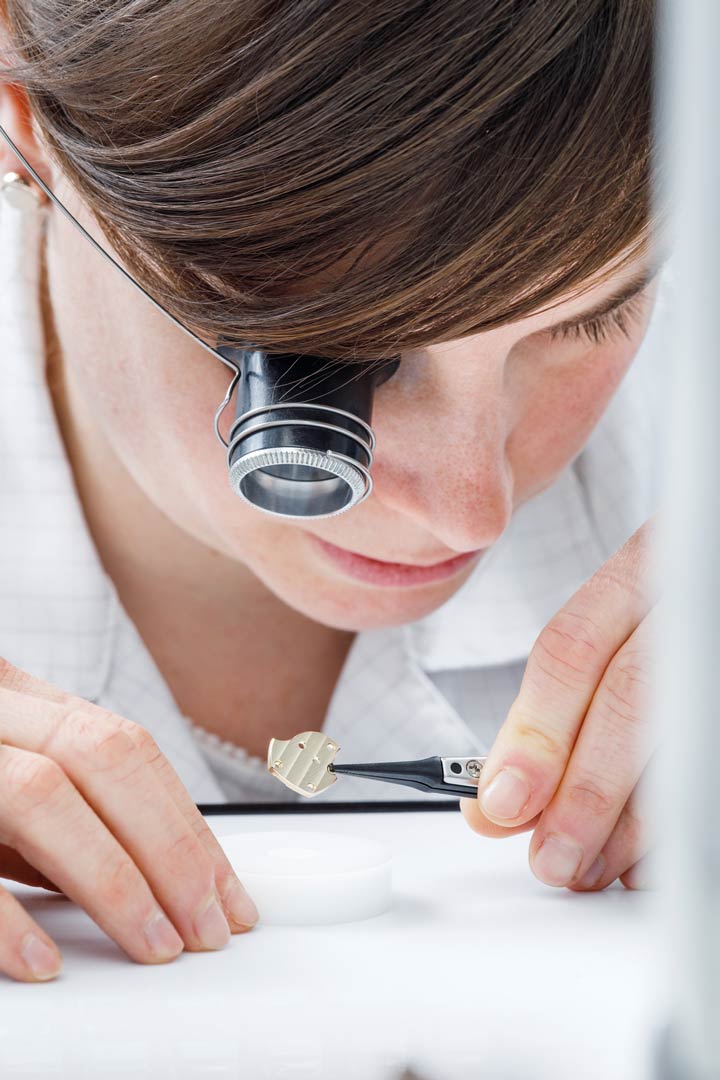
Polishing
Embellishing every part of a movement makes every Armin Strom watch akin to a hand-crafted piece of jewelry.
Working bare brass or steel by hand is time-consuming work: edges of plates, bridges and levers must be perfectly chamfered or, as watchmakers call it, beveled. Every part is then polished to perfection, even when the embellishment won’t be visible in the finished watch.
Beveling and polishing requires a trained eye and fingertip sensitivity together with both patience and perseverance. For example, even a relatively small part like a pallets bridge will require at least half an hour to complete – and often more than that.
Traditional Grinding
Here a classic fine watch-making finishing technique known as “Geneva Stripes” (Côtes de Genève), is displayed. They’re created via the use an abrasive disc that’s applied in perfectly straight lines to create the Côtes de Genève on the workpiece.
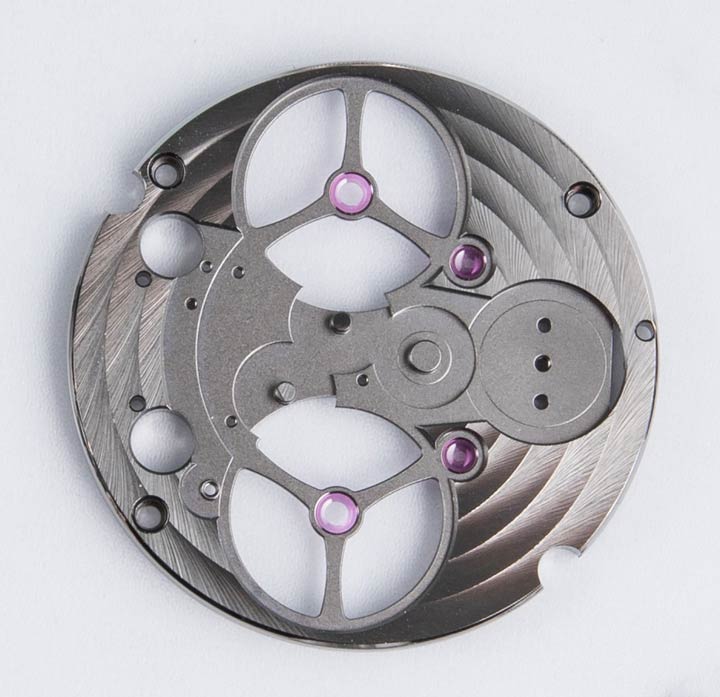
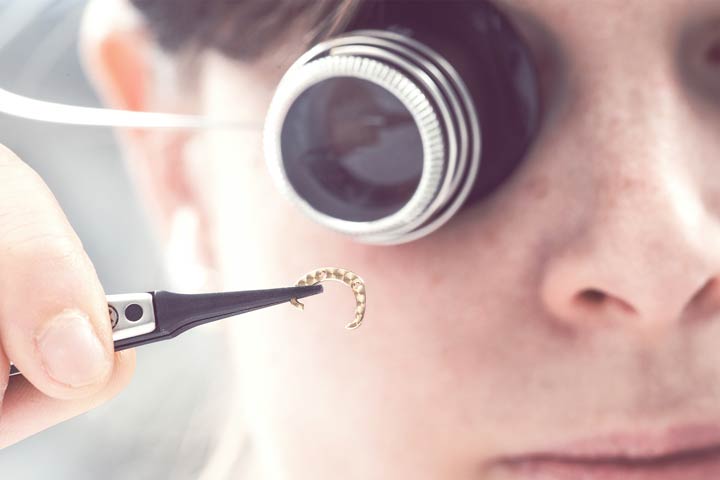
Circular graining (Perlage) is a decorative motif reminiscent of clouds, typically used on main plates. To achieve this pattern, the watchmaker uses an abrasive pencil and gently makes contact with the workpiece, gradually working across the whole surface. This creates the characteristic overlapping circular grained motif.
All rotating parts of an Armin Strom movement are embellished with a circular grinding pattern.
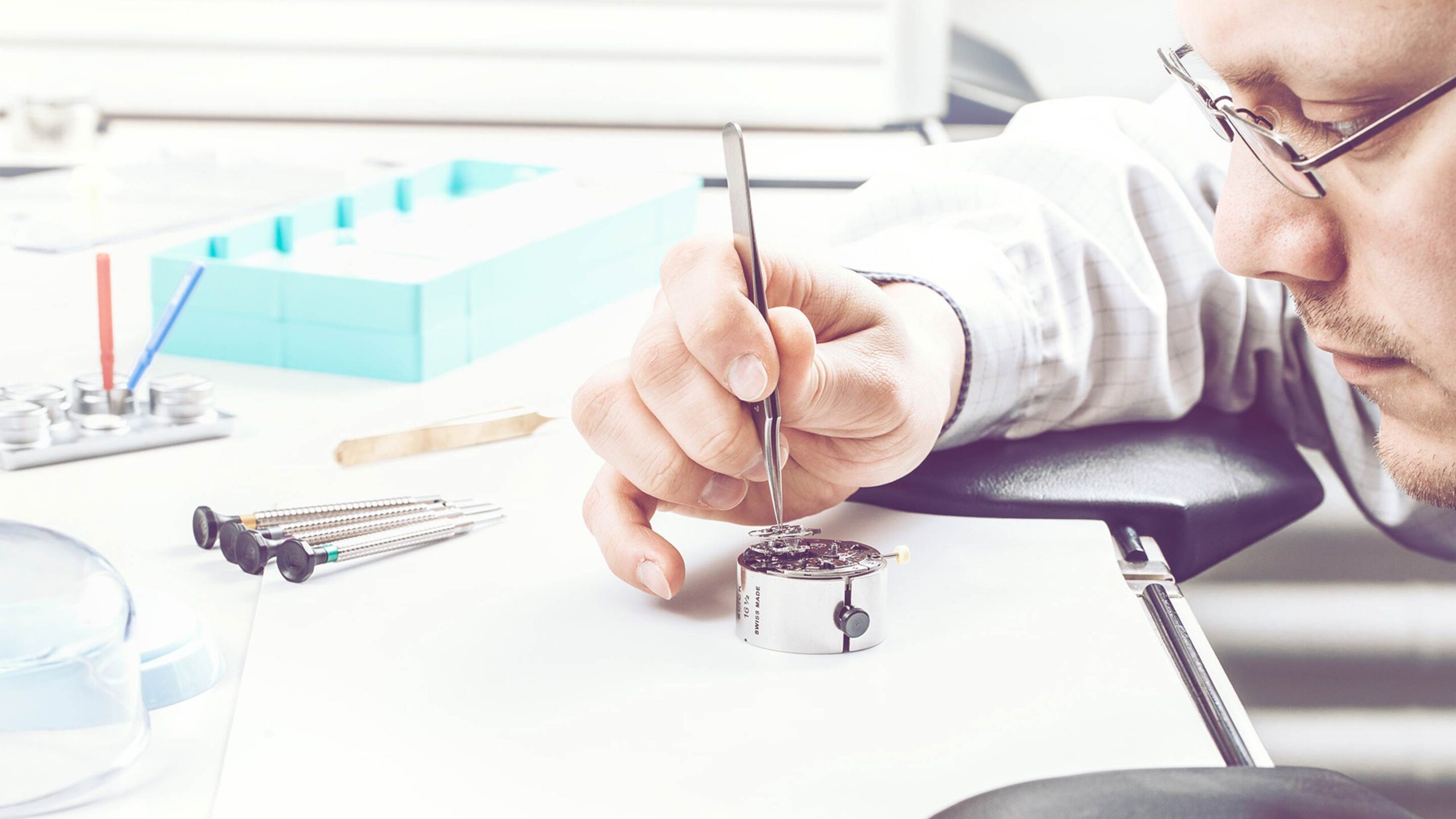
Assembling
A watch comes to life.
Up to this point, they were all just individual parts – turned, milled, polished and decorated. Now the watch will begin to take shape.
The watchmaker uses a pressing tool to insert the jewel bearings for the spindles of the toothed wheels into the plate and bridges. This is a crucial operation. The way the jewels are pressed in influences the correct vertical play of the gear-train. Do the gear-wheels and pinions mesh together correctly? Does the height need adjusting by a few hundredths of a millimeter? Once the gear-train is adjusted, the bridges and plates are screwed down, and the mainsprings are assembled in the going barrels, then the movement is ready to receive the escapement. With the installation of the escapement, consisting of the escape-wheel, the pallets and balance-wheel, the watch comes to life.
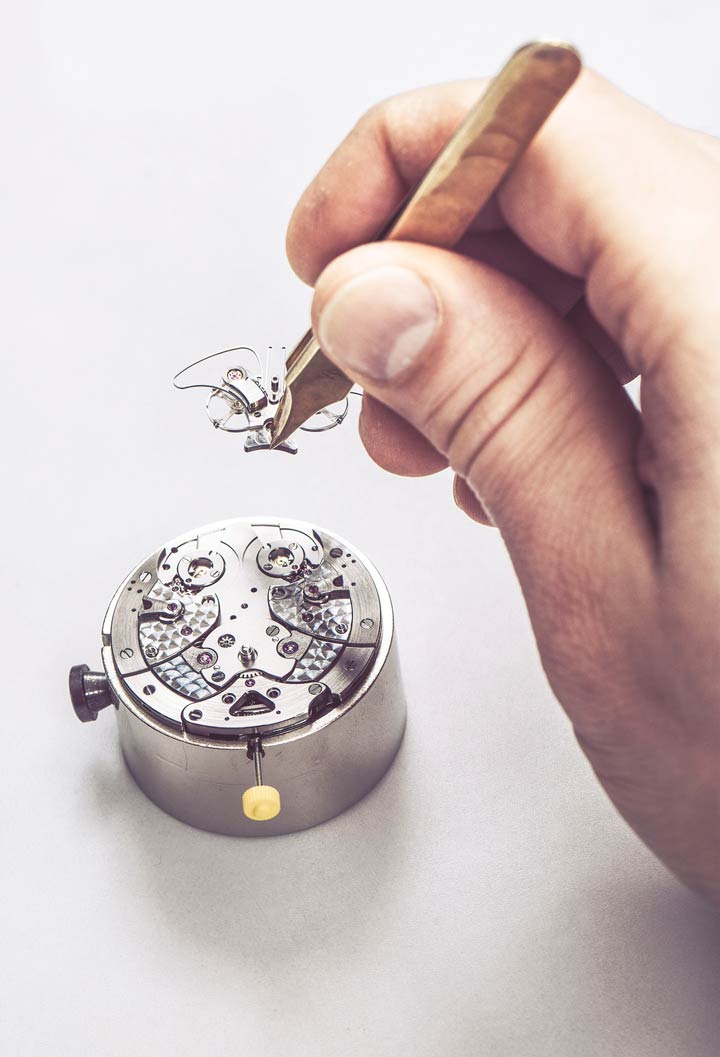
Every movement is assembled twice
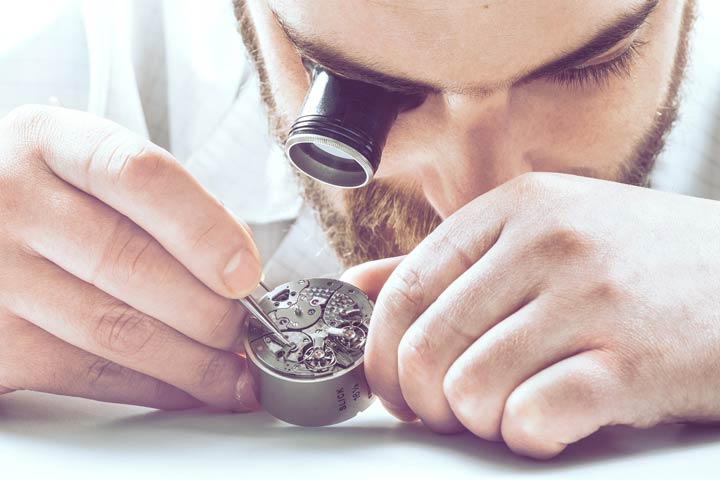
After the first assembly, the movement is completely disassembled and each individual part is then cleaned, dried, reassembled and lubricated. After the second assembly, the movement is meticulously regulated before the watchmaker sets the hands and re-inserts the movement back into the case. The back of the case is then fixed in place. The completed watch is subjected to a multi-day rate test on a watch winder. Water resistance is also tested. Once the watch has passed these quality tests, it is finally certified as complete.